Andon board: real-time monitoring & process optimization
An Andon board is a digital display board for real-time monitoring of production processes. It visualizes errors, machine status and production progress and ensures greater transparency in production. With a modern Andon system from Peakboard, you can minimize production downtime and optimize processes.
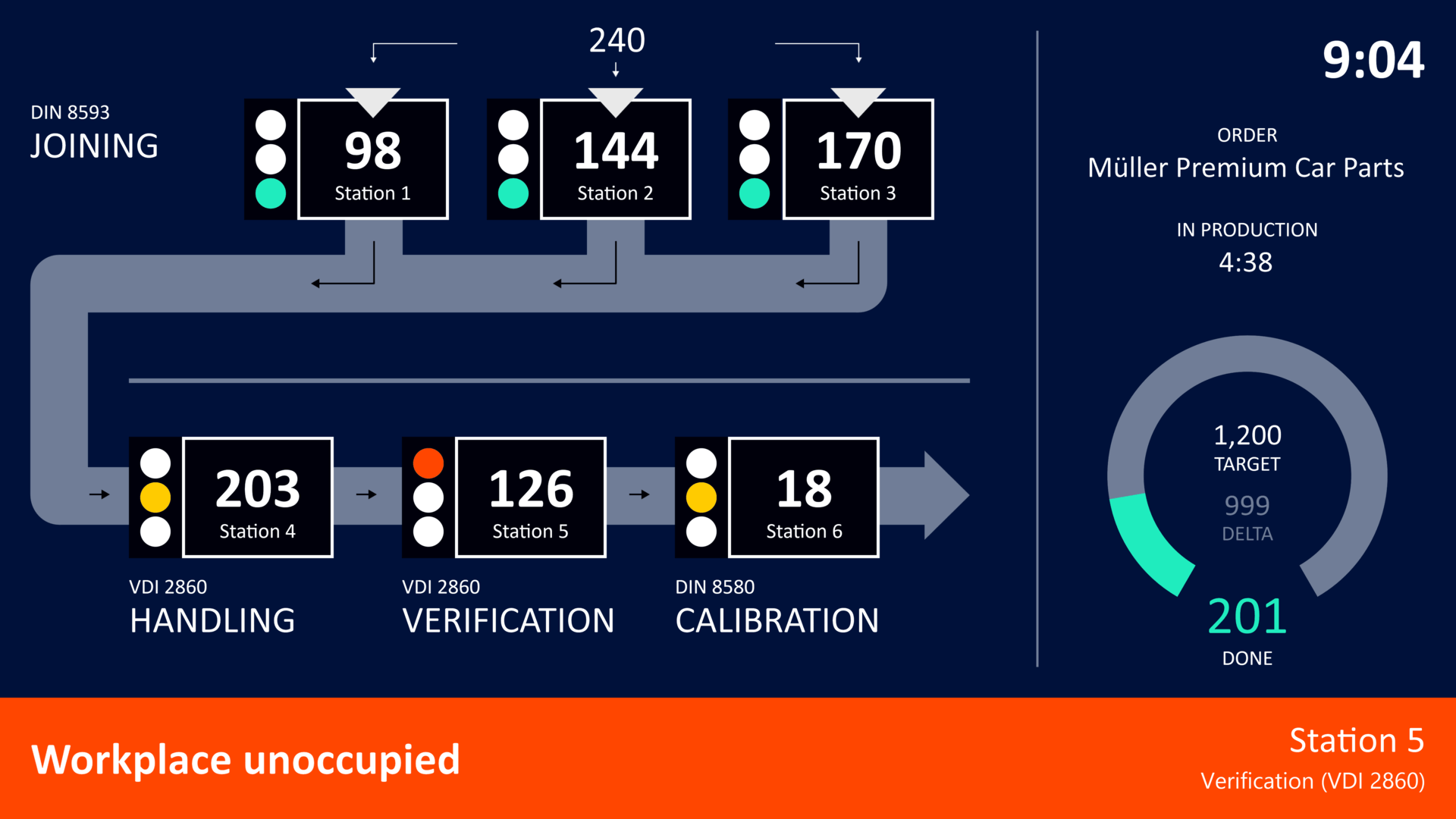
A step ahead with a smart Andon system
Keep an eye on your production in real time, react immediately to faults and optimize processes efficiently. Peakboard ensures greater transparency, less downtime and maximum efficiency.
Challenge
- No real-time insights into production
- Delayed responses to disorders
- High manual effort for data evaluation
Solution with Peakboard
- Real-Time Data Visualization & Monitoring
- Automatic alerts in case of discrepancies
- Intuitive dashboards for a better overview
Result
- More transparency & faster decisions
- Less downtime & reduced costs
- Optimized processes & higher efficiency
Benefits of an Andon board
Production downtime and inefficient processes can result in significant costs. A digital Peakboard Andon Board helps to identify problems at an early stage and to counteract them efficiently. The continuous display of relevant information gives both machine operators and managers a clear overview of the current status of production. This makes it possible to immediately identify deviations in the process, to keep an eye on production goals and to initiate necessary measures directly.
In addition to real-time error detection, an Andon board also improves team collaboration. Employees can act proactively because they are always informed about current developments. This reduces unnecessary downtime and increases productivity sustainably.
The most important features of an Andon board
A modern Andon board offers a variety of functions that depend on a efficient production monitoring and process optimization aim. The visual presentation of machine status and production figures provides clarity and ensures quick troubleshooting. Through the Integration into existing systems Like ERP or MES platforms, data can be processed and reused seamlessly.
In addition, a digital Andon board enables:
- Instant fault detection through real-time data
- Optimizing production processes through transparent visualization
- Reducing downtime through faster responsiveness
- Automated or manual interaction using touch screens or buttons
- Integration of signal lamps for visual warning in case of faults
This is how the Andon system works
An Andon system consists of several core components which, in combination, enable efficient control and monitoring of production:
- Andon board: Visually displays the current production status and makes deviations immediately visible.
- Andon light: Uses a traffic light system (green, yellow, red) to indicate the status of machines or processes.
- Andon cord (emergency line): Enables employees to manually report a malfunction and thus trigger an immediate response.
With a digital Andon system from Peakboard Production data can not only be visualized, but also edited interactively. Users can decide which key figures are shown on a display and whether the dashboards change automatically. This creates a dynamic, adaptable solution, which can be optimally integrated into existing production environments.
Key figures on an Andon board
An Andon board provides valuable insights into the production process by relevant KPIs (Key Performance Indicators) clearly presented. These include:
- Overall equipment effectiveness (OEE): A key figure for measuring production output.
- Cycle times: Comparison of target and actual values to identify deviations.
- Downtimes & error rates: Key indicators to reduce production losses.
- Production progress & goal achievement: A clear presentation of ongoing manufacturing processes and set goals.
These KPIs enable companies to continuously analyze processes and achieve long-term efficiency gains.
Andon board with peakboard — the ideal solution
With Peakboard A flexible and individually adaptable Andon solution is available to you. Integration into existing machines and systems is easy, which ensures seamless integration into the manufacturing process. Peakboard also offers:
- One intuitive visualization of important production figures
- Interactive control options via touchscreen or button
- data write-back in ERP or MES systems for always up-to-date data
- Integration of signal lamps to visually support processes
Von Industrieexperten genutzt
um Abläufe clever zu vereinfachen.
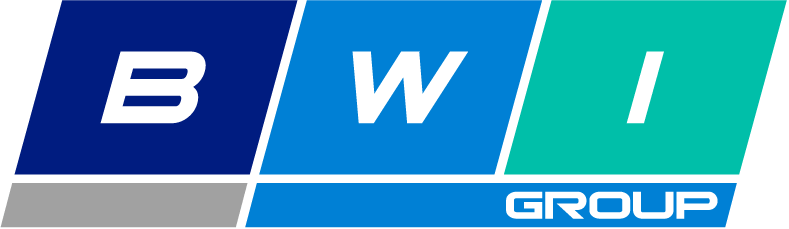
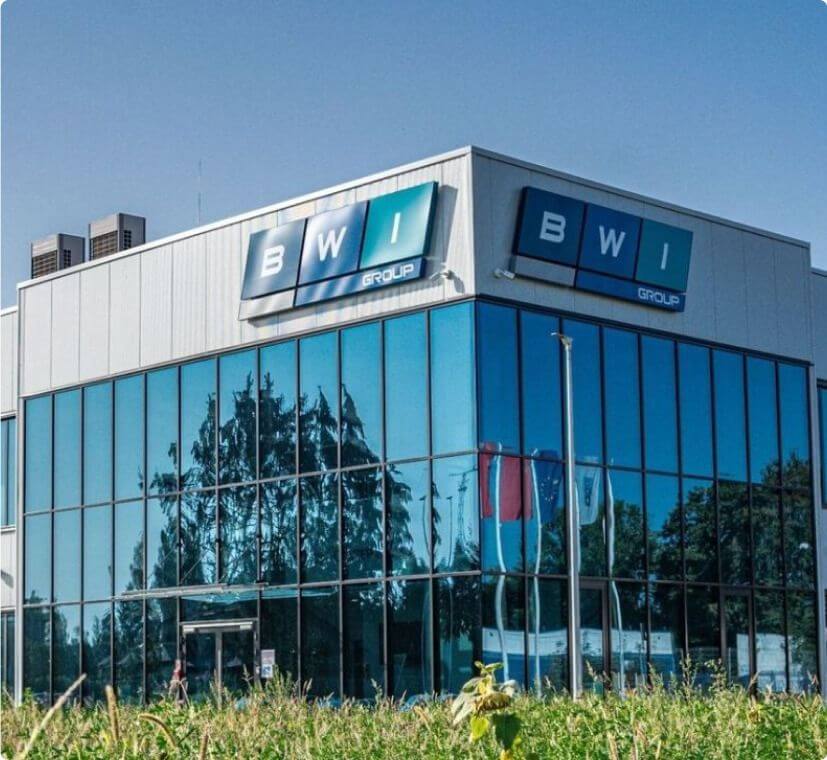
“Using Peakboard has improved our quality, increased efficiency and motivated employees. The implementation was extremely fast. Overall, it was a small step with a big impact.”
The software
Start now for free with Peakboard Designer
Capture, process and visualize production and order data in real time — simply and without programming knowledge.
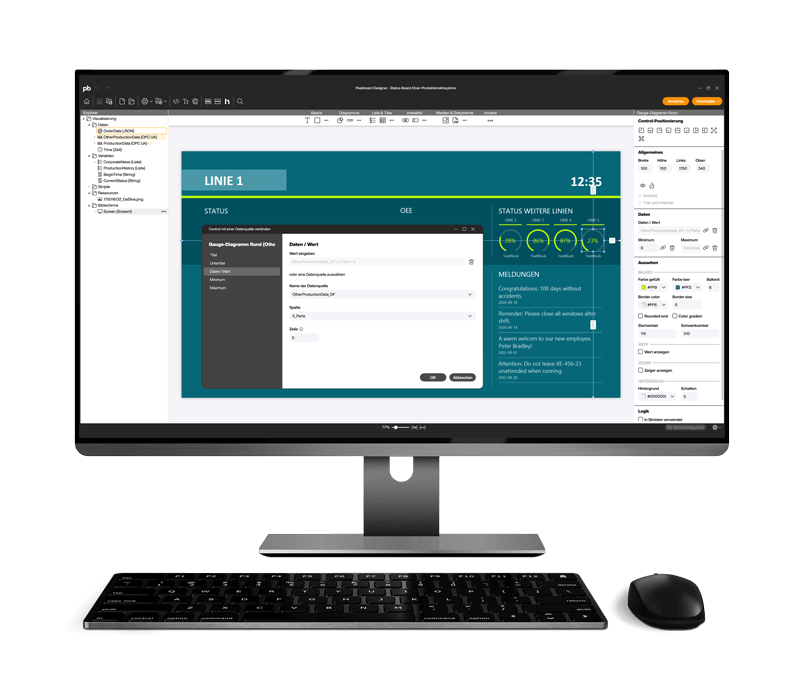