Real-Time Data Visualization for Increased Productivity
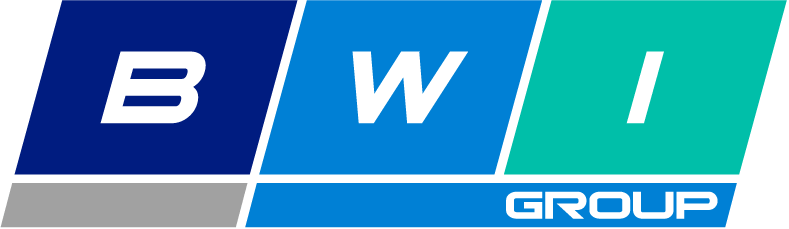
BeijingWest Industries (BWI Group)
challenges
The visualization of OPC UA data to display the status of several machines; in addition, the solution must also function as an MES system
solution
Integration of Peakboard at Individual Stations in the Company to Visualize Production Data in Real Time
benefits
- Agile planning thanks to real-time data
- Quick implementation and easy integration of all required data sources
- Higher employee motivation through transparency about their own work performance
Time to Value
A working day to create the first dashboard and integrate it into the system
BWI Group is a full-service provider of chassis, suspension and brake products for the automotive OEM market, which began in Dayton, Ohio, USA. Today, the company is a leading developer and manufacturer of innovative premium dampers and magneride-controlled suspension systems, brake calipers and electronic stability control systems for the global transport market. Many products are completely manufactured in-house, from raw material to the end product.
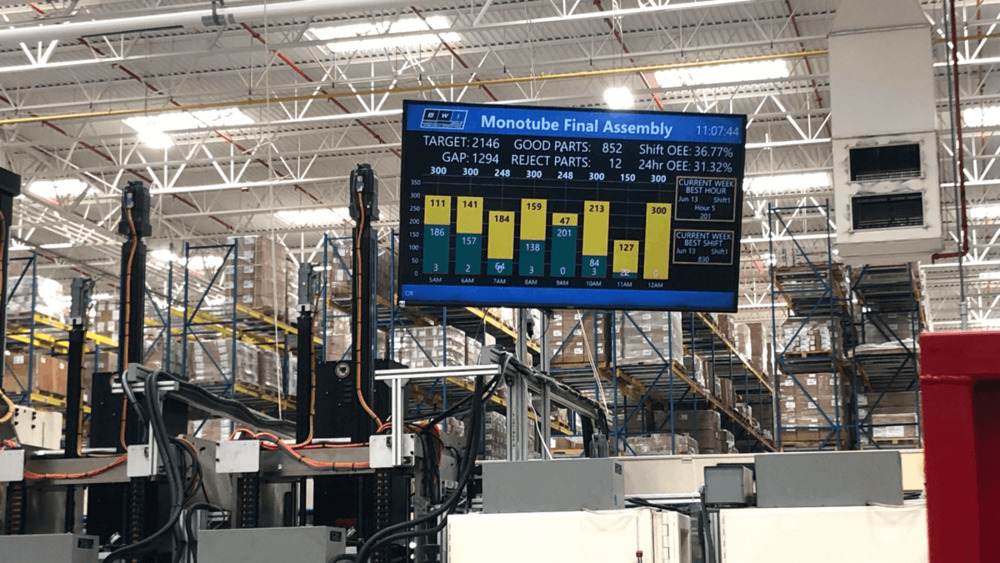
Peakboard dashboard at BWI Group: Real-time visualization of production data for greater efficiency, transparency and optimal OEE on the shop floor.
“Using Peakboard has improved our quality, increased efficiency and motivated employees. The implementation was extremely fast. Overall, it was a small step with a big impact.”
Take the numbers to the people
BWI is first looking for a solution for visualizing OPC UA datato view the status of multiple machines. In this way, the company wants to present the actual output on the production line and obtain information about good and bad parts, production goals, shift duration and other production-related components. Kepware's OPC UA server provides the actual values and a simple Excel file provides the target values. The data is updated every 8 minutes in the cloud and every 15 minutes locally. The company waits up to 24 hours for the results of a shift.
In the course of the decision-making process, it becomes apparent that the solution should also have MES properties.
“The systems used in the company so far were not flexible enough and did not allow any interactive inputs. As a result, the data was not up to date, we were unable to plan agilely and the employees working shifts had no knowledge of the current state of production at the end of the shift,”
Explains Jordan Marlin, Operational Technology Manager, Industry 4.0 Engineering at BWI.
Easy deployment, fast results
Jordan and his team come across Peakboard and use the free Peakboard Designer in advance.
“We needed almost no support to design the Andon boards. With the tutorials, videos and documentation provided by Peakboard, we acquired the knowledge independently,” explains Jordan. “In particular, the impressive templates in Peakboard Designer due to their simplicity were very helpful.”
The company's OPC UA Kepware server is connected to the Peakboard Box. Peakboard could also directly access the PLC of the individual machines and therefore does not require a Kepware server, but harmonizes with it so that the source connection is even faster. Thanks to the structured available data, BWI can transparently present KPIs such as OEE, cycle and shift times within a few minutes. About OPC AND OTHERS The real-time values go to the dashboard, and the Kepware Server also stores them as a history in an SQL database for more in-depth BI analysis. Without a Kepware Server, Peakboard Hub could do the job.
Shift managers can enter target values, breaks and shift times via an interface and thus communicate new orders or other information immediately and dynamically calculate the time required. This Interactive process Provides shift management with a precise overview and visualizes the data for employees on the shop floor, giving them a targeted insight into the production status. In this way, target and actual conditions are displayed on all assembly lines in the plant every 10 seconds and all parties involved are equally informed. This has resulted in a gamification approach: The employees on the best shifts and hours per week are visibly rewarded and incentivized on the dashboards.
Opex across the board
After successfully completing the test phase, Peakboard is integrated at the individual stations in the company. The boards have now been in use for two years.
“Employees used the visualization right from the start and now understand better how live knowledge of production data improves our processes,” says Jordan. “Employees rely on the dashboards, check their plausibility and, if necessary, give me immediate feedback. This shows that the information there plays a central role in their everyday work. There is a new culture of responsibility that makes work easier for everyone.”
The electronic calculation of shifts is reduced from up to 24 hours to real time, the amount of Missing parts significantly reduces. In addition, decision-making processes are streamlined and management acts faster.
Peakboard worldwide
BWI wants to transfer the solution to various locations such as Mexico, Poland, the Czech Republic and China. In addition, should Shopfloor Boards Are used in Greenfield, which display news and weekly schedules. In addition, Peakboard Edge is integrated into the existing system, which makes it possible to visualize production and logistics data that is not yet available digitally.
Start now with Peakboard and simplify your processes
Turn live data into smart decisions — with Peakboard.