Smart factory made easy
Corratec
challenges
Lack of overview of the system conditions of the electric monorail, the current production output compared to the specification and the assembly progress of the individual assembly lines
solution
Create an info board with Peakboard that combines and visualizes all data sources available on the shop floor
benefits
- More production efficiency through rapid problem identification and agile intervention
Time to Value
Less than a week
Even companies with 200 employees can quickly and easily — often even without comprehensive external advice — visualize their production in real time and thus optimize their processes. Bicycle manufacturer Corratec proves that joining a smart factory is easier than expected.
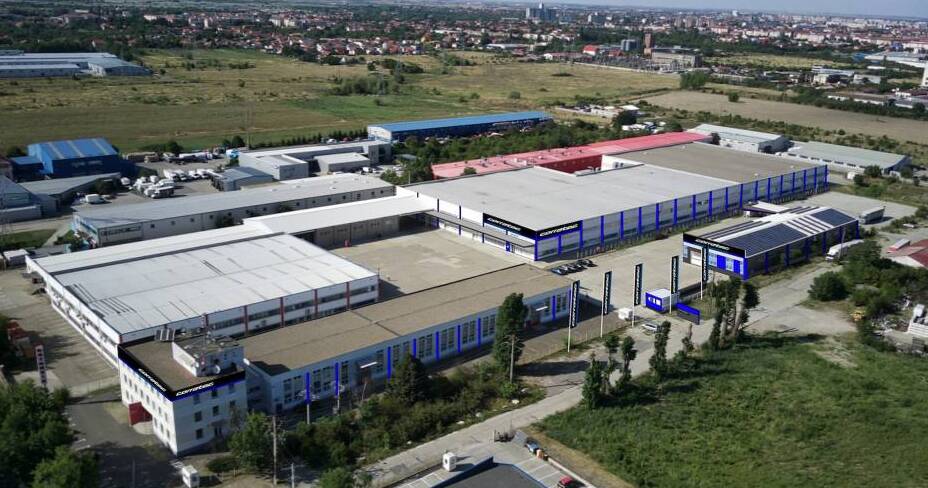
“We created the dashboard ourselves: download the Peakboard Designer, select the components to be displayed, order and set up the Peakboard Box. With knowledge of automation structures, it was easy. There was also a lot of learning by doing and it was fun,” says Sagberger. “The first implementations were up and running after just one week. ”
Inaccurate, incomplete, and delayed
Since 1990, Corratec has been manufacturing high-quality bicycles for all purposes at its Raubling site in Bavaria. This is done via an electric monorail on a rail under the roof. There are a total of 12 assembly lines on which quantity assemblers work in concert. The existing visualization, which measures output and daily output, is a single-user solution that can only display PLC data with 10-minute evaluation times.
For its production lines, the company wants to create an information board that includes everything on the shop floor Merges data sources and visualizes. Those responsible are looking for a simple, open dashboard solution so that they can independently make adjustments in the form of additional data sources and their own developments. In addition, investment costs should remain within a defined framework.
“We also want to see what we're doing, i.e. flexibly visualize data from different systems and bring it together on a board,” says Ralph Sagberger, summarizing the challenge. “Our PLC, the S5 from Siemens, was the crux of the matter: We had a display of the data on proprietary software from the local manufacturer. But the presentation of delivery times and prices did not fit, and no changes were possible. ”
Programme-free drag and drop solution
Corratec requires a system with ready-made modules that can be dragged and dropped without programming effort can put together. In Peakboard, Sagberger finds such a solution that allows him to quickly create a dashboard.
“The decisive factor for Peakboard was ultimately the costs, the intuitive operation and the ability to connect many interfaces,” summarizes Sagberger.
Self-directed dashboard
Corratec opts for visualization at assembly and production management level and not directly on the assembly line. The frequency of updates is between real-time — for information from the S5 — and cyclical database queries in ranges of seconds. There are interfaces to:
- Siemens S5 via OPC (electric monorail)
- MS SQL server (production database)
- MS Dynamics AX (ERP)
“Connecting the PLC was no problem. Adding a Microsoft AX system was more challenging, but still possible without external support,” explains Sagberger.
The dashboard visualizes the System states the electric monorail, the current production output compared to the requirement and the Assembly progress of the individual assembly lines. The 12 production lines and the transverse trolleys that control the supply of the electric monorail are shown. Their condition, loads and destinations are visible at a glance. Production management can also see the numbers of the vehicles currently passing by and a queue for buffering. Processing times at workstations round off the information to form an overall picture.
More production efficiency through rapid problem identification
With real-time data visualization, Corratec has a digital production control system received. The company records the state of production at a glance and immediately recognizes any problems that arise. This allows it to intervene agilely and plan better. Before Peakboard was used, the current state of production had to be actively queried by means of an evaluation in Excel.
“We are more efficient because we can now see all running lines in real time. In the past, we had to go for a lot of walks to get an overview, which delayed the processes,” concludes Sagberger, who therefore reflects on the use of further dashboards at master level.
Start now with Peakboard and simplify your processes
Turn live data into smart decisions — with Peakboard.