Increasing delivery reliability with real-time applications
Hermes Schleifmittel GmbH
challenges
A lack of prioritization of production orders led to delayed processing of time-critical orders.
solution
Introduction of Peakboard at the Uetersen site to display the order processing sequence, to map relevant production KPIs and to display internal information.
benefits
- Real-time dashboards create transparency in order priority
- Easy connection of various data interfaces, including SAP and Qlik
- “Bulletin board” provides an overview of KPIs (e.g. delivery reliability, output, waste, etc.) and discloses production results from the previous day
Time to Value
Founded in 1927, Hermes Schleifmittel GmbH is a family-run company based in Hamburg. As a manufacturer of bonded high-performance abrasives and abrasives on surfaces, Hermes serves customers worldwide, including from the metal and woodworking industries. Whether functional, aesthetic, matte or brilliant surfaces: With over 1,500 tool variants, the company offers an extensive product portfolio and thus guarantees high-quality results for every grinding process. Today, the company employs around 1,000 people, 100 of whom are employed at the Uetersen site in Schleswig-Holstein.
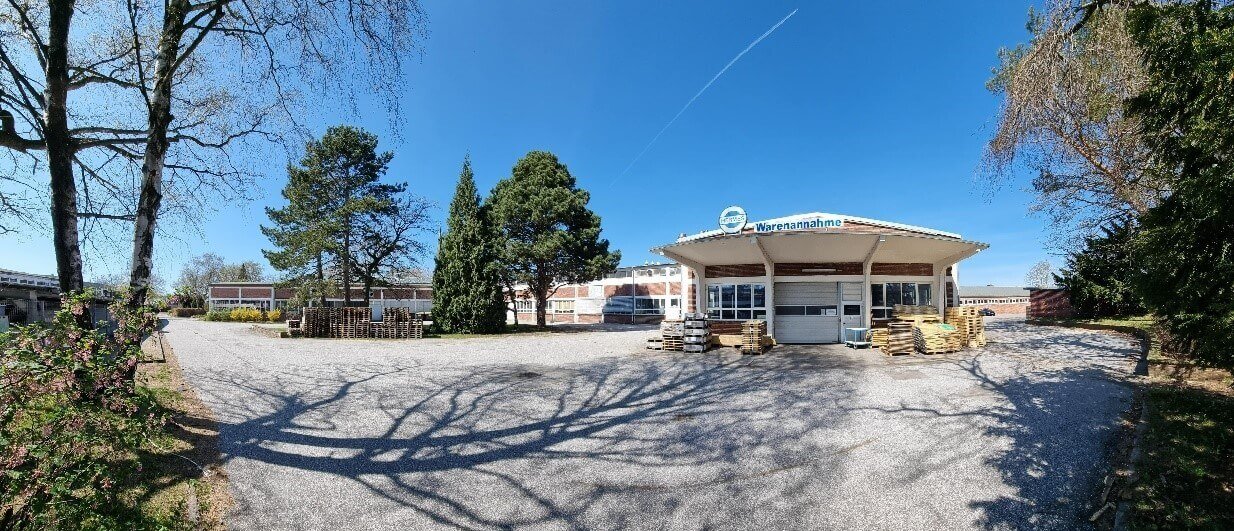
“Our main goal was initially to significantly reduce delivery times and at the same time increase delivery reliability so that our customers are guaranteed to receive their orders on time.”
Tracking and prioritizing production orders was difficult for production employees in Uetersen. At their workplaces, there was no way to see the current production status. In addition, incoming orders were not accepted according to priority, but rather arbitrarily.
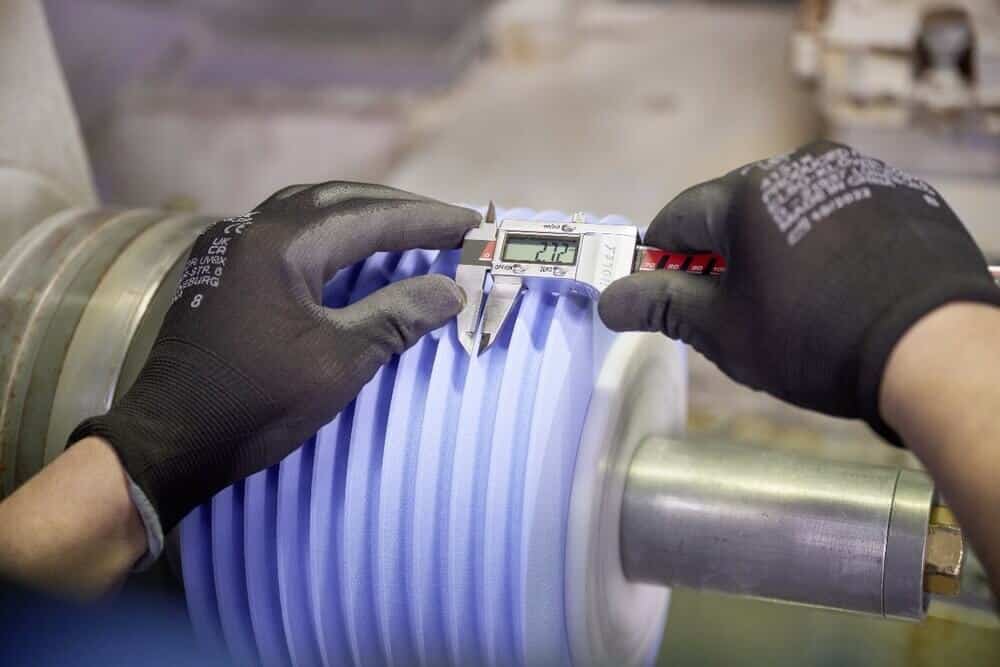
“There were a large number of orders at the plant and employees tended to pick out just about any task. As a result, more complex or time-critical orders were repeatedly not carried out on time,” explains Sven Russmeyer, plant manager at Hermes.
The lack of transparency in the processes also frustrated the teams. As a result, they had no opportunity to find out about the production and objectives from the previous day. However, a specific assessment of the objectives at the start of the shift is essential for process optimization. In order to increase transparency in production and improve internal communication, digitization measures had to be taken.
Create transparency of KPIs with an appealing designer
The search for the right solution finally came to a successful end at Peakboard, a provider of a low-code platform for creating individual industrial applications. The company immediately noticed the appealing design of the Peakboard Designer, the software for creating the applications:
“Compared to other systems, Peakboard Designer allows you to display applications in a very appealing and vivid way. This is very well received by employees,” According to Russmeyer.
Another reason why Peakboard was chosen was the easy connection of various data interfaces. Even before working with the Stuttgart-based software provider, Hermes was already using SAP and Qlik as pre-systems to process the data. These systems were finally connected to the new system. In addition to presenting the order processing sequence, the solution is also used to display relevant production KPIs and to display internal information.
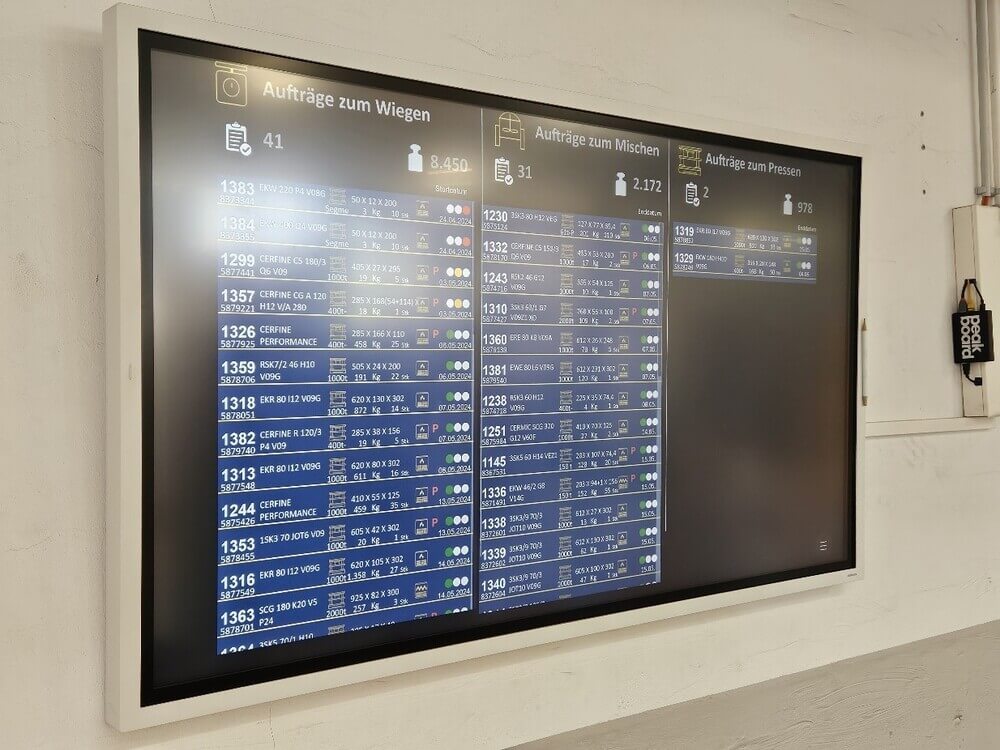
Peakboard dashboards bring light into the dark
With the Peakboard solution, Hermes covers a total of three applications. The first use case is in production: Here, the workshop is equipped with a Peakboard Box, which visualizes central order management on a screen in real time and uses color markings to determine its priorities and presents them in a visually appealing way. Prior to working with Peakboard, the individual production orders were recorded via SAP, but employees at the workshop had no opportunity to view the timelines of the respective orders.
But Hermes uses Peakboard's solution not only in production. In the second use case, another connected screen in the entrance area of the company serves as a kind of bulletin board for employee information. This allows staff to get an overview of KPIs, including delivery reliability, output and scrap, at the start of the shift. In addition, the teams of employees here discuss the previous day's production results every morning and exchange views on how they can use the available data to achieve the goals for the next shift. If the workload of employees in the individual departments is unbalanced along the value stream, their deployment can be managed centrally. In this way, personnel resources can be used more efficiently. When Hermes receives a customer visit, the solution also serves as a welcome screen in the third use case.
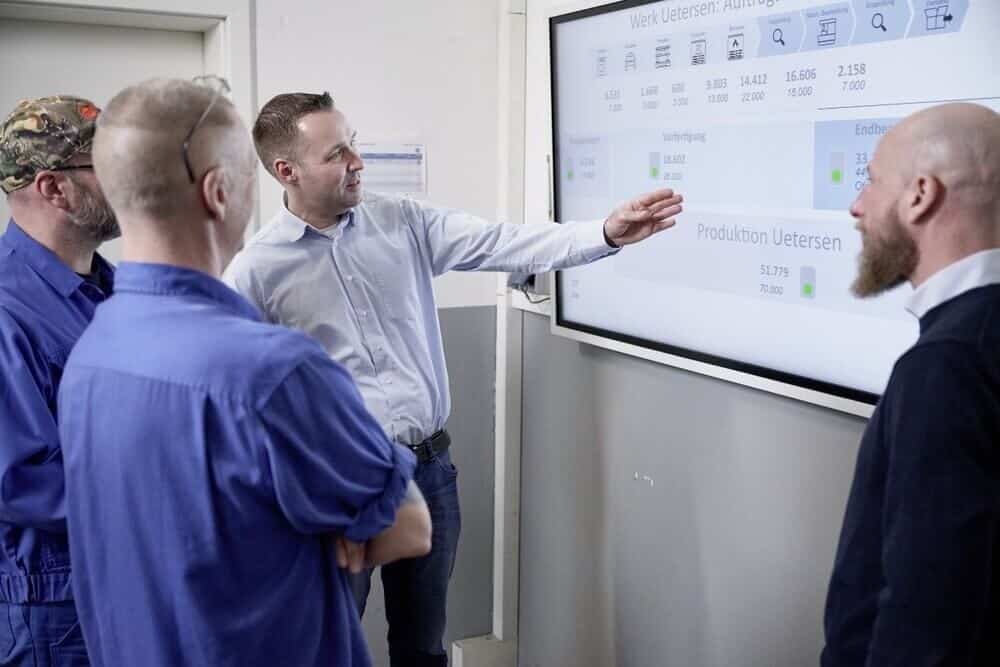
Further expansion planned
Hermes is currently using five Peakboard Boxes at its Uetersen site. They are used to transparently present the above-mentioned KPIs, the processing sequence of orders and internal communication. The dashboards are also transferred to interactive touch screens, which switch between different display boards when tapped and reveal other relevant key figures. Consideration is already being given to expanding the three use cases.
“Peakboard's digitization solution has resulted in employees tackling highly prioritized orders first, reducing delivery times and increasing delivery reliability.”, Russmeyer summarizes the project.
Start now with Peakboard and simplify your processes
Turn live data into smart decisions — with Peakboard.