Real-time data usage — to the dashboard in less than two days
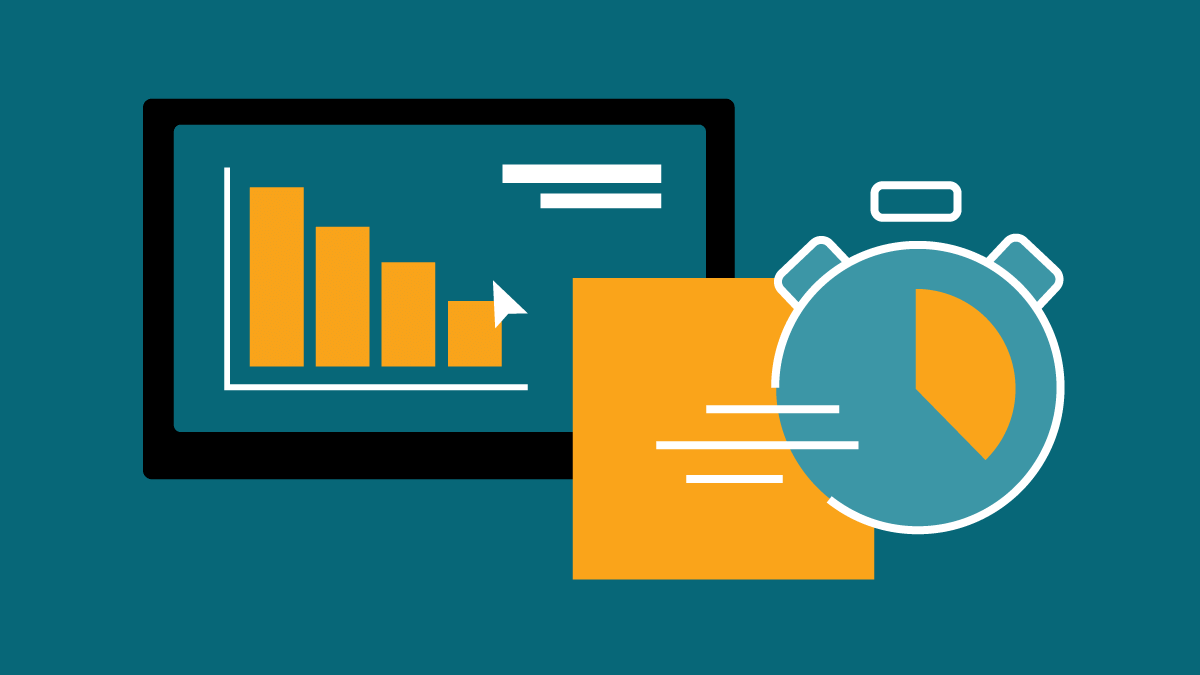
Easy access to real-time data
At first, many companies do not know exactly how to start using their data in real time and shy away from the supposedly large financial and personnel costs. There are solutions that supplement the existing IT infrastructure without having to meticulously plan for months and provide many resources for subsequent changes. One to two days of preparation is usually enough to implement a functional dashboard that shows you a current target/actual comparison. For example, you can minimize downtime after just a short period of time, plan resources better, use workers more efficiently, or let employees report their success.
The problem: Data that is too old, which is often only available in a scattered way
We know it: Until a product is finished, it goes through several production steps, which must work together smoothly. If there are disruptions during one of the production steps, many companies often only react slowly because they receive the information too late, sometimes even the next day. This makes efficient intervention in ongoing processes impossible, especially as managers and employees often have to log on to a computer first in order to obtain the information they need to optimize processes.
It would be better if the news about an important event was automatically communicated to exactly the employees who need the information right at the time it happened. This is made possible by monitors in the production hall, for example, which display process-relevant information in real time and thus allow you to take action immediately and directly on site.
You can implement such a real-time data dashboard in just a few steps. Once learned, the process of creating such a dashboard can be easily repeated at any time as needed, for example when changing production processes require new information or your ideas about which data should be output and how improve.
Ideally, specialist departments are able to quickly adapt their dashboards themselves accordingly and design more without seeking help from an external or internal third party. Changes then no longer affect network integration, as all work takes place exclusively on the software interface of the visualization solution. The Peakboard Designer interface, for example, is intuitive to use even for people who don't use it on a daily basis. But now for the specific steps for your real-time data dashboard:
Step 1: Define your goals and select the data and recipients
As a rule, a very well-functioning dashboard can be developed in just a 2-hour workshop with all people involved in this process. In addition to network administrators, this includes employees who later read and interpret the information from the dashboard, such as the workforce on the assembly line, and, of course, the specialist department itself.
First, determine what you want to achieve. After you have defined the goals, you determine which information should be used to achieve them. The following questions will help you with this: Which information influences the process in which way? And: Which actions can be derived from the information? It is then defined which persons should receive which data.
Tip: The wealth of available data sometimes makes you want to pack too much into a single visualization. Superfluous information prevents you from quickly recording the really important elements on your dashboard, as it quickly makes it confusing. Remembering regularly what exactly each piece of information contributes to achieving the goal helps you focus.
Step 2: Select a visualization solution and clean up data
The solution that you ultimately choose should not only serve to achieve all goals, but at best save IT resources. Peakboard does not require any external servers and meets the necessary security requirements by only temporarily storing the data and encrypting communication. In addition, communication only takes place within the local network, so that no data is transferred to the outside world. It is also important that communication between the visualization solution and the network is limited to the data that has been explicitly approved for it.
As IT infrastructures have often grown over the years, data is usually available from an ever increasing number of sources. These range from Excel lists to machine control, sensors or low-voltage signals, to MES, production control systems or SAP. The data that the systems generate for various status messages is correspondingly different. In order to be able to display them intelligently later, you clean them up and bring them into a common logic.
In multi-stage production, for example, identifying downtimes is crucial. To do this, we at Peakboard work with internal IT specialists: They know where the required data is and what the corresponding error message looks like, because each system displays the message “Machine is standing” differently, for example. If the error code is known, it is corrected. This means that it is rewritten or freed from unnecessary information in such a way that the visualization solution can recognize and process it.
Step 3: Design visualization and implement solution
The collected ideas should finally be implemented in a dashboard. It is important that the dashboard is not only nice to look at at the end, but above all provides relevant information so that viewers can derive instructions for action from it. Use the entire space of your dashboard, but don't overpack it, as described above. The right amount of white space, grid alignment, and a legible font also make the dashboard look neat and understandable. You can find more tips and tricks for designing a perfect visualization in our blog post “Dashboard Design Basics”.
Your finished visualization can now be placed where you want it to be used later. A dashboard that is intended for an individual workplace should ideally hang at eye level with the observer. A standard monitor is sufficient for this application. A dashboard that houses relevant information for the entire shop floor is best placed in a central location and preferably displayed on a large screen. In this way, the information displayed on it can also be recognized from a distance.
conclusion
The dashboard creation process described here can be transferred to many different areas of a company. For example, display availability at outgoing goods, create a welcome board for reception or visualize real-time information about company-relevant data in controlling or management.
There are usually three small steps between the desire and reality of real-time data visualization in a maximum of two days. If you bring everyone involved together, you will quickly find a dashboard supported by everyone. At a later stage, specialist departments can independently adapt or optimize it to new circumstances, according to their needs — but without having to get IT on board.
What does my finished dashboard look like?
Whether it's a receipt dashboard, production dashboard or logistics dashboard — you decide exactly what your finished dashboard looks like. Our templates show you a few examples:
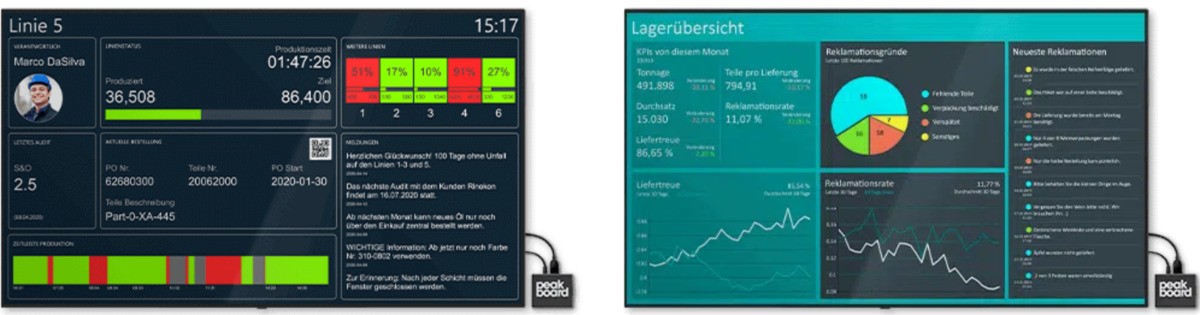