Optimize turnaround time by 40 percent
Bizerba SE Co. KG
challenges
Analog management methods for assembly lines offered no way to precisely record the actual production time per work step. This also led to challenges in precisely recording cycle times and production processes as well as in identifying sources of errors and delays.
solution
Integration of a complete Manufacturing Execution System (MES) into existing structures for complete digitization of the assembly line.
benefits
- Processing time per product reduced by 40 percent
- Increasing efficiency through RFID scanning
- Reduced error rate
Time to Value
A working day to create a proof of concept with a focus on machine monitoring. Just two months after integration, Bizerba was able to start the production phase.
Bizerba SE & Co. KG looks back on a long history: founded in 1866, the company is now one of the world's largest manufacturers of scales, cutting machines and labeling solutions. Whether it's self-service scales in supermarkets, slicers in restaurants or the correct labeling of products in the food industry or in logistics centers — the family-owned company offers a comprehensive portfolio of hardware, software and services. With over 40 subsidiaries, Bizerba is active in 120 countries and generates an annual turnover of around 800 million euros. In addition to the headquarters in Balingen, Baden-Württemberg, Germany also has a production site in Messkirch.
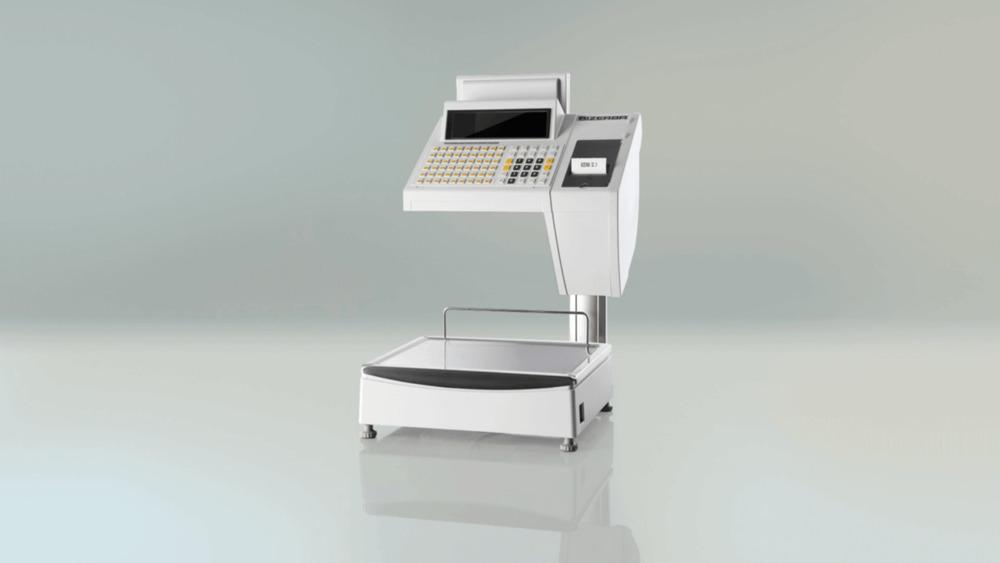
“At first glance, the complete digitization of our processes appeared to us as a mammoth task. However, we quickly realized that this change was a decisive step towards operational excellence. ”
Pen and paper are out
In the past, Bizerba has always assigned orders to staff in paper form at the Messkirch site. Employees were asked to extract their daily tasks from a special box and process them manually. However, this method offered no way to precisely record the actual production time per work step. Taking into account the working practices of the time, a target production time was set. However, this did not fully take into account the individual efficiency of employees and the performance of the machines. The previous paper-based organization therefore led to challenges in precisely recording cycle times and production processes as well as in identifying sources of errors and delays. In order to optimize these processes, Bizerba has taken a groundbreaking step: implementing a completely digitized solution that has replaced pen and paper.
Peakboard covers various areas of application
“At first glance, the complete digitization of our processes appeared to us as a mammoth task,”
Yasin Öztürk, Digitalization Project Manager at Bizerba, remembers the final decision to switch over.
“However, we quickly realized that this change was a decisive step towards operational excellence. ”
The search for a suitable solution finally ended at Peakboard GmbH from Stuttgart, a provider of a low-code platform in an industrial environment. The decisive factor for this decision was the consistently positive experience that Balingen headquarters had already had with the Stuttgart-based company and its solution for creating industrial applications.
At the first meeting with Bizerba Messkirch, Peakboard first created a proof of concept tailored to the company's requirements with a focus on machine monitoring. This showed that the solution based on the Peakboard Box, the hardware component with the operating system, and the Peakboard Designer, the software component with the configuration software, was able to meet the requirements. Here, the orders that pass through the respective system were tracked and it was determined how many orders actually go through per day. This process was successfully established within one day. Over time, the collaboration went beyond pure machine monitoring and solutions were sought that would also optimize other areas of application.
Have products on screen at all times
In order to digitize the entire assembly line, Peakboard has integrated a complete Manufacturing Execution System (MES) into the existing structures. This covers a total of four assembly lines, each with four workstations, and tracks various work processes. However, there is a particular focus on tracking the products. In order to be able to trace them at any time, Bizerba uses RFID tags, which are recognized by scanners below the assembly line. The read data is automatically stored in the Peakboard Hub, a central server that manages all data. Three lists are stored here, which contain information about machines, employees and errors. The current order status can now be determined from these data sources.
As soon as the RFID system registers a product at the workplace, the predefined production time begins. If planned interruptions such as meetings or breaks occur automatically during this time, these are automatically deducted from production time so as not to falsify the actual production time. In the event of unforeseen error messages such as quality defects or missing parts, the employee can report them immediately via a barcode scanner connected to the Peakboard Box. The Peakboard Boxes are the hardware components of the Peakboard solution and transfer the data to the Peakboard Hub. In this way, the origin of the error can be traced back and the cause of the error is also transparent.
Real-time tracking reduces assembly times.
By tracking the OEE of the machines and the productive working time of employees, the production times set by Bizerba could be reduced by 40%. So that shift managers can also get a quick overview of the current status of all assembly lines, a screen is installed in the assembly hall, which provides the current OEE of the machines and the efficiency of (anonymized) personnel at a glance. By historicizing the collected data, it was possible to identify the most common errors. With this knowledge, processes could be optimized and the error rate reduced.
Just two months after integration, Bizerba was able to start the production phase. In addition to the short configuration phase of the solution, customers particularly appreciate the leeway they use to make independent changes to the applications in the system. Since the system is based on the flexible low-code platform developed by Peakboard, target times or shift plans can be edited and adjusted by the company without in-depth IT knowledge.
Digitalization as a door opener
Digitalizing complete assembly lines can bring many benefits to a company. Bizerba has achieved a significant increase in efficiency by introducing precise machine control using RFID scanning. Sources of error are stored and historicized in the Peakboard Hub so that long-term measures can be developed to prevent errors. Real-time monitoring of the manufacturing process and the OEE of the systems has also reduced target working time by almost half. The easy handling of the low-code-based Peakboard solution enables the company to intervene in the system independently. The applications can be changed at will without in-depth IT knowledge.
Start now with Peakboard and simplify your processes
Turn live data into smart decisions — with Peakboard.