In 10 steps to digital shop floor management
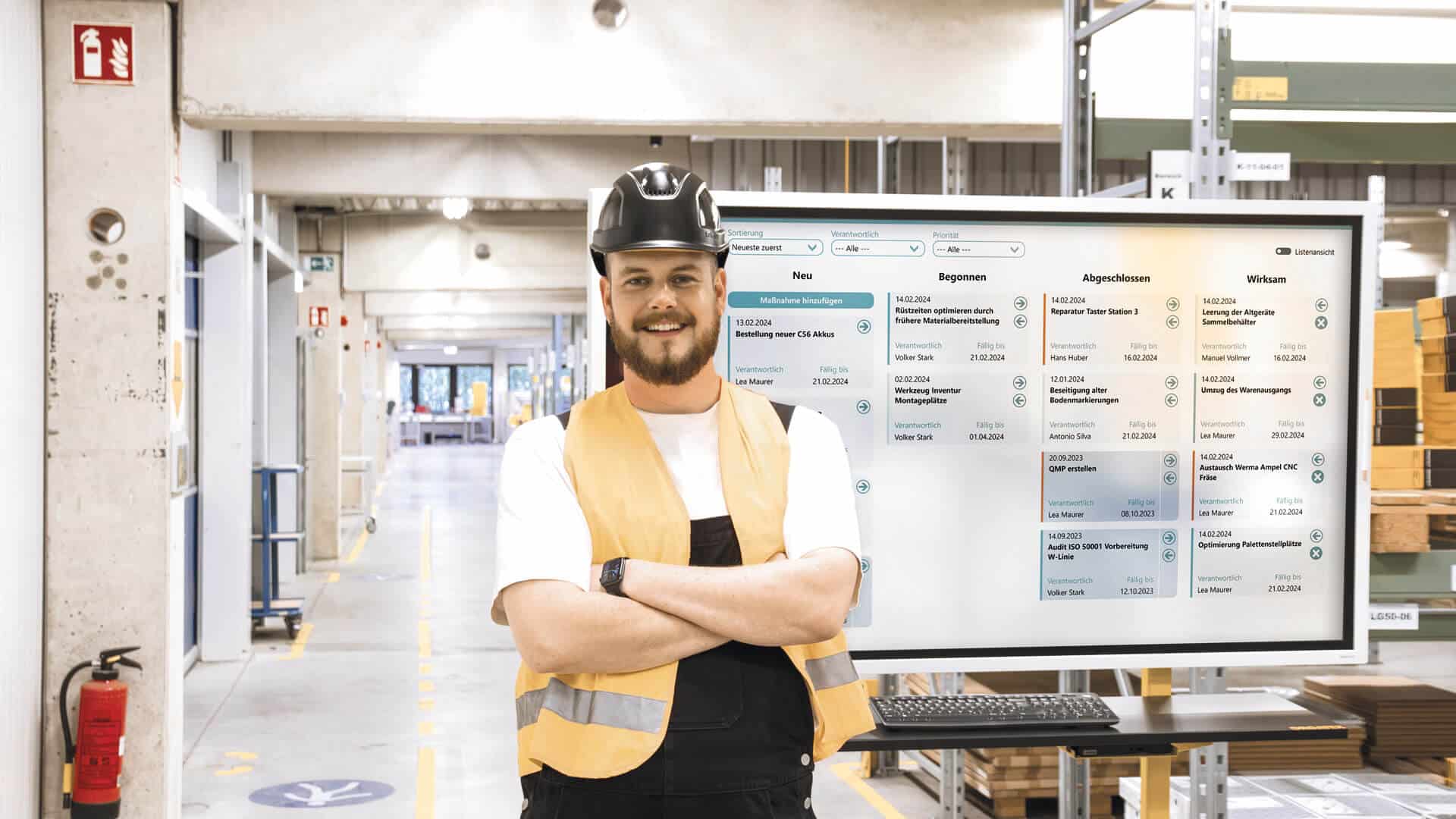
1. Current situation analysis and definition of objectives
Start with a detailed analysis of the current processes on the shop floor. Identify weak points, inefficient processes, and digital improvement potential. Define clear goals for digitization, such as increasing productivity, improving quality control, or increasing flexibility in production.
2. Select appropriate technologies
Find out about digital technologies that can support your shop floor management. These include IoT (Internet of Things) devices for real-time data collection, software for production management and mobile solutions for employee communication.
solutions such as Apexboard also offer a clear, central view of the shop floor and provide an easy introduction to shop floor management. A transparent, central overview provides immediate clarity and enables direct recognition of process status and performance. When ongoing processes are transparent, analyzing them and initiating improvement measures is easier. This means that Apexboard supports you right from step 1.
3. Involve employees
Digitalization affects all employees on the shop floor. Involve them early in the process to address concerns, get feedback, and promote acceptance. Training and workshops can help prepare employees for upcoming changes.
4. Start pilot project
Implement the selected digital technologies first in a limited area or for a specific product line. This makes it possible to test the solutions, make adjustments and assess the effects on the processes before a full rollout takes place.
With Peakboard as a low-code platform for industrial applications, you can always start small and with a use case and scale later as needed. Minimal risk with maximum flexibility.
5. Ensure data integration
For successful digitization, data must be able to flow seamlessly between different systems and devices. Make sure that the digital solutions used are compatible with each other and that a central data platform such as Peakboard is used, on which all relevant information is collected. The highlight: Peakboard already provides the necessary interfaces to your systems.
6. Optimize processes
Use the data obtained through digitization to continuously analyze and optimize processes on the shop floor. This can be supported by automated data analyses, AI-based decision-making tools and real-time feedback loops.
7. Implement security and data protection measures
With the introduction of digital technologies, the risk of cyber attacks and data breaches is also increasing. Implement robust security measures and follow applicable privacy policies to protect data and systems.
8. Continuous monitoring and feedback
Effective digital shop floor management requires continuous monitoring and adjustment. Use Apexboardto track performance indicators and make improvements based on employee feedback.
9. Scale and expand
After successful completion of the pilot project, you will begin gradually expanding the digital solutions to other areas of the shop floor. Take into account the experiences and findings from the pilot project to optimize the process.
10. Fostering a culture of continuous improvement
The digitization of shop floor management is a continuous process. Foster a culture of continuous improvement in which employees are encouraged to contribute new ideas and participate in the continuous optimization of production processes.