No way to buy a new one! Stay fit for the future with Retrofit
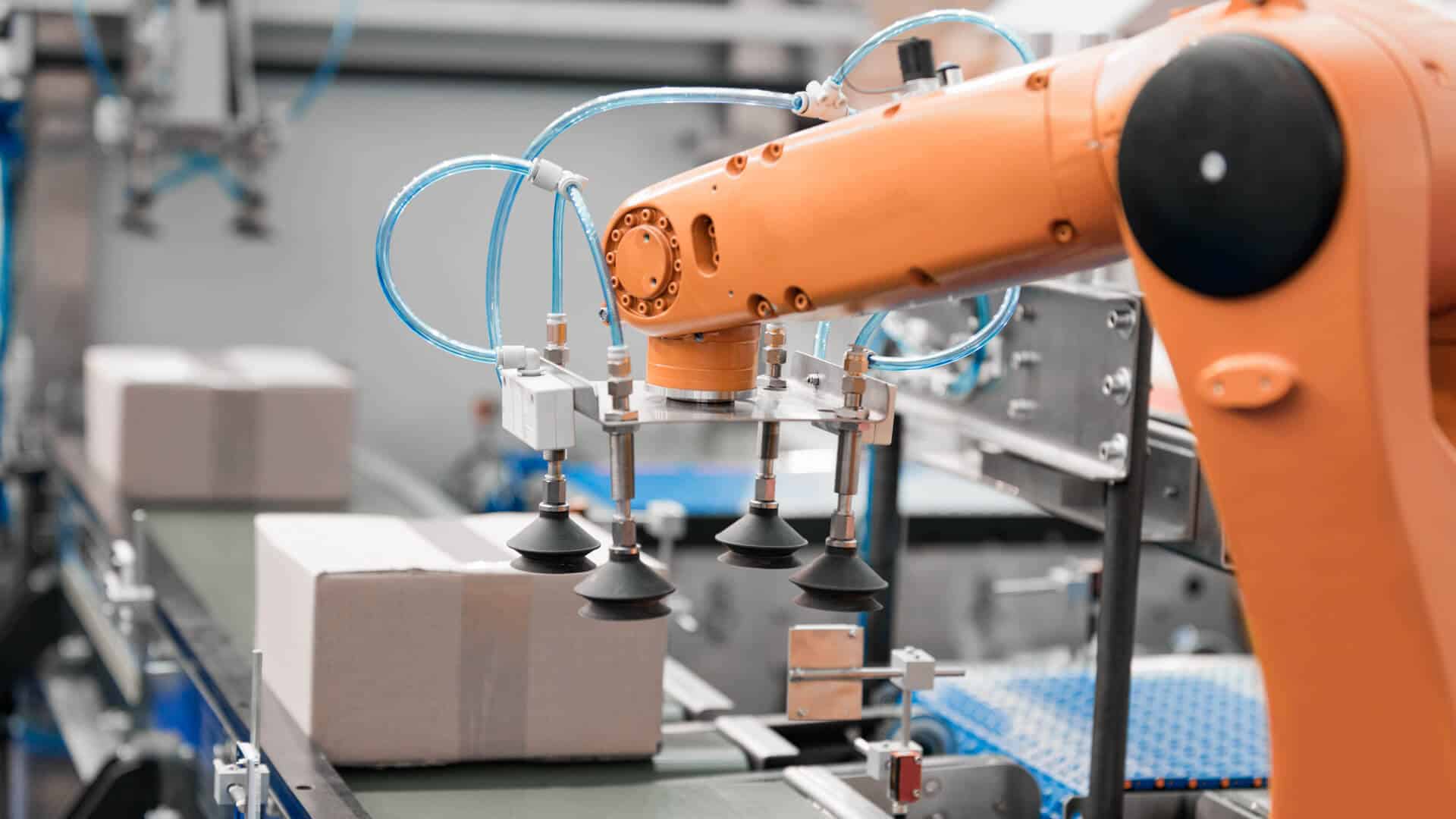
The older machines can do a lot. Only data unfortunately not
Companies often use older machines that only provide data in analog form. For example, they can typically emit 24-volt interference signals, which a simple traffic light system uses to indicate defective cables. What they lack, however, is information about changing temperatures, fluctuations in boiler pressure or, due to a lack of a piece meter, the flow rate. Older devices also often do not meet the requirements for transferring the data to a database. This issue also affects many newer machines. However, shop floor managers also need this information in order to obtain a correct, complete picture of their own production and to make optimal decisions.
All machine manufacturers cook well — but only their own soup
Another problem is that production machinery is constantly being expanded, for example with new production lines. However, many companies use models from different providers with low connectivity between each other. As a small island, each speaks its own language. The lack of a common denominator creates significant communication gaps.
New purchases or classic retrofitting? usually very expensive up to expensive
At the same time, the pressure to modernize is increasing. Digital real-time images of our own production and logistics are now a competitive factor. The most obvious solution is to replace existing machines. However, this rarely makes economic sense. Retrofitting is correspondingly popular. Anyone who retrofits in the traditional way must accept extended downtimes due to the conversion and risk that the machine will not work afterwards. After retrofitting, there is also no automatic improvement between all machines. In addition, any intervention in the controller (PLC) jeopardizes the manufacturer warranty and CE certification.
Retrofitting with Peakboard — without programming
The central challenge in digitizing a machine environment that is heterogeneous in terms of age and connectivity standards is avoiding IT costs. With Peakboard, companies can make their information that is not yet available digitally as data for other applications without using up IT resources.
To give a simple but effective example: A light barrier installed on the production line, which is connected to Peakboard, forms a digital real-time piece counter. The same goes for a temperature meter. These are just two examples of many. Of course, Peakboard can also visualize all other existing data.
With the right data, even business intelligence works
Companies can also historicize the data in order to analyze it as part of their business intelligence. This enables them, for example, to identify clusters of errors in individual lines based on average values. They are able to connect numerous other systems with maximum flexibility, for example to link order data from SAP with real production data.
Peakboard therefore provides real-time data for the agile live optimization of production or logistics processes and can also save this as a starting point for strategic decisions. We have already supported hundreds of customers in this way, from corporations to SMEs.